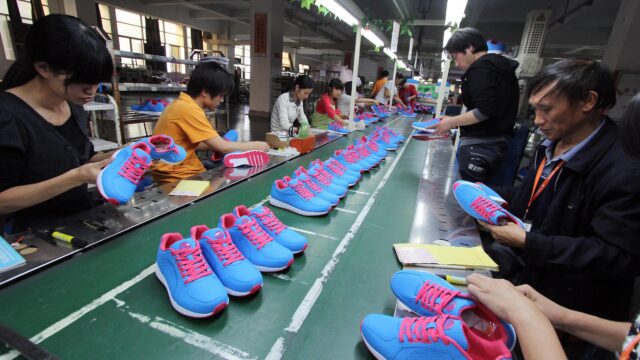
A New Era for US Shoe Manufacturing: Can it Thrive Without Cheap Labor?
In a significant move for the American manufacturing landscape, Keen, a family-owned footwear company, is set to open a new factory in Kentucky just outside Louisville this month. This development aligns with the “America First” economic strategy that gained traction during the Trump administration, symbolizing hopes for a manufacturing revival that has often been elusive.
However, the narrative surrounding Keen’s new factory reveals a more nuanced picture of the current state of manufacturing in the United States. With only 24 employees on the floor, Keen’s factory is primarily automated, relying on advanced robotics for tasks such as fusing soles and trimming materials. This shift signifies a transformation in manufacturing dynamics, moving away from traditional labor-intensive methods to capital-intensive, technology-driven processes.
The Cost of Labor and Automation
Hari Perumal, Keen’s Chief Operating Officer, elaborates on the financial challenges of manufacturing in the U.S., stating, “The labor rates here in the US are very expensive,” with wages in American factories reaching 10 to 12 times higher than those in Asia. This reality prompted Keen to shift some of its production to domestic sources back in 2010, a strategy that has provided a buffer against tariffs imposed during the recent trade tensions.
Yet, the journey towards local production is fraught with complexity. The global supply chain remains intricately tied to shoe manufacturing, with a vast majority of footwear still produced by hand in Asian countries, leading to billions of pairs being imported into the U.S. each year. Keen’s strategy has involved significant investments in automation, allowing its Kentucky plant to operate with a remarkably reduced workforce compared to traditional overseas factories.
The Broader Challenges of Reshoring
Keen’s experience is not unique. Prominent brands like Nike, Adidas, and Under Armour have also explored establishing manufacturing capabilities on American soil over the past decade, often without success. Currently, Keen only assembles about 9% of its shoes in the U.S., highlighting the ongoing struggle to produce footwear efficiently at scale domestically.
Historically, American manufacturing boomed post-World War II, giving rise to a robust middle class with factories producing everything from shoes to cars. However, the late 20th-century shift towards globalization saw many industries move overseas to capitalize on cheaper labor, resulting in the erosion of the nation’s industrial base and contributing to the socio-economic disparities still evident today.
Attribute | Details |
---|---|
U.S. Labor Cost | 10-12 times higher than in Asia |
Percentage of Shoes Made in U.S. | Approx. 1% |
Keen’s Domestic Assembly | 9% |
As for Keen, its commitment to American production has been a long-term investment that its family-owned status has allowed. “We are a private, values-led company,” notes Perumal. “We can make decisions without the pressure of quarterly results.” Nevertheless, even companies like Keen face the harsh reality that reversing decades of globalization is no simple task.
Looking Ahead
The new factory opens a window into what the future of American manufacturing could look like, where tradition intersects with technology. Amidst the hurdles and challenges, it raises a crucial question: can manufacturing thrive in the U.S. without the reliance on cheap labor? With the right investments and innovations, the answer may become clearer in the years to come.