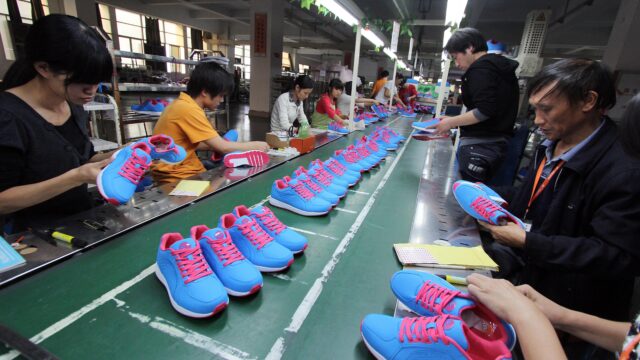
Challenges of U.S. Shoe Manufacturing in an Automated Age
In the suburb of Louisville, Kentucky, Keen, a family-operated shoemaker, is set to inaugurate a new manufacturing facility this month. This expansion aligns with the “America First” economic initiative, embodying hopes of revitalizing domestic manufacturing—a promise that has often remained unfulfilled.
However, Keen’s factory serves as a microcosm reflecting the complexities of modern American manufacturing. With a workforce of only 24 employees, the plant relies significantly on automation, employing advanced robots that handle tasks such as fusing soles and trimming materials. This shift highlights a significant evolution in production methods, moving away from labor-intensive processes to high-tech, capital-heavy operations.
A Costly Reality
According to Keen’s Chief Operating Officer, Hari Perumal, the expensive labor rates in the United States pose a significant challenge. He notes that U.S. labor costs are roughly 10 to 12 times higher than in Asian factories. Amidst rising expenses in China, Keen began its journey of reshoring production in 2010. This decision has provided a buffer against tariffs imposed during the Trump administration, though it came with its own set of complications.
The global nature of footwear production remains a hurdle, as the vast majority of shoes—around 99%—sold in the U.S. are imported from countries like China, Vietnam, and Indonesia. Keen has adopted an aggressive approach towards automation to make domestic production economically feasible, allowing the Kentucky plant to function with a fraction of the manpower employed overseas. “We are making products here in the USA very economically and very efficiently,” states Perumal, illustrating the reliance on automation in their manufacturing process.
A Broader Perspective
The challenges of reshoring extend beyond Keen. Prominent brands such as Nike, Adidas, and Under Armour have attempted to introduce innovative manufacturing technologies in the U.S. over the past decade but faced significant obstacles. Currently, Keen assembles only 9% of its footwear domestically, revealing the complexities associated with scaling production effectively.
The landscape of American manufacturing has witnessed profound rises and gradual declines. Post-World War II, U.S. factories produced shoes, appliances, and automobiles, employing millions and fostering a robust middle class. However, globalization in the late 20th century catalyzed the relocation of many jobs abroad as companies sought cheaper labor and fewer regulations. This shift has decimated the U.S. industrial sector, creating ongoing political and economic tensions.
Manufacturing in the U.S.: A Dwindling Ecosystem
For most U.S. shoe companies, the path to domestic production is rife with challenges. Pepper Harward, CEO of Oka Brands—a rarity among U.S. footwear manufacturers—shares insights on these difficulties. His factory in Buford, Georgia, produces for brands like New Balance and Ryka. Harward notes the ongoing struggle to procure affordable components and materials locally. “It’s not a self-sustained ecosystem,” he explains, underscoring the obstacles of navigating supply chains that frequently change.
Aspect | Detail |
---|---|
U.S. Labor Cost | 10-12 times higher than Asia |
Percentage of Shoes Made in the U.S. | 1% |
Keen’s Domestic Production | 9% of shoes assembled in the U.S. |
For companies like Keen and Oka, American shoe production demands significant investment, patience, and strategic innovation. Tariffs and pandemic-induced supply chain disruptions have amplified interest in local manufacturing; however, Harward remains dubious about the possibility of a significant return to domestic production. He estimates that even with favorable tariffs, only around 6% of manufacturing might return to the U.S.
As Keen’s long-devised plans materialize, the company exemplifies the kind of commitment often associated with family-owned businesses. Perumal notes, “We are a private, values-led company,” underscoring their ability to make long-term decisions without the pressure of quarterly results. Ultimately, Keen’s factory represents not a revival of traditional manufacturing but a vision of what lies ahead—where advanced technology and age-old craftsmanship coexist in a redefined American manufacturing landscape.