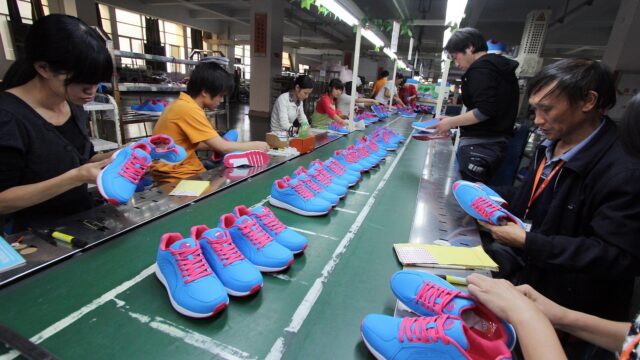
Manufacturing Shoes in the US: A Complicated Journey
In a small town near Louisville, Kentucky, Keen, a family-owned shoe manufacturer, is set to launch a new production facility this month. This initiative reflects a broader “America First” economic policy that was notably supported during the Trump administration, aiming to restore American manufacturing. However, the reality behind this move uncovers the complex and evolving nature of production in the United States.
A Modern Factory with a Tech Twist
At its new facility, Keen employs only 24 individuals, relying on advanced automation technologies like robotics to streamline production processes. These intricate machines assist in tasks such as fusing shoe soles and assembling materials, showcasing a significant shift in manufacturing methods. The once labor-intensive sector has transitioned into a capital-intensive, technologically-driven field.
Hari Perumal, Keen’s Chief Operating Officer, explains, “The labour rates here in the US are very expensive,” comparing them to those overseas, where manufacturing costs can be 10 to 12 times lower. This reality prompted Keen to explore domestic production as early as 2010 due to escalating costs in Asian factories. Such a decision has afforded the company a protective buffer against tariffs imposed under the previous administration.
Global Supply Chains Remain a Challenge
Despite this initiative, Keen only manufactures 9% of its footwear in America. The shoemaking industry remains deeply entrenched in extensive global supply chains, with nearly all footwear sold in the US sourced from countries like China, Vietnam, and Indonesia. The domestic supply chain for footwear is nearly non-existent, with less than 1% of shoes being created on American soil.
Pepper Harward, CEO of Oka Brands, acknowledges these hurdles, stating, “It’s not a self-sustained ecosystem.” His Georgia-based factory, which produces for brands like New Balance, struggles to consistently find affordable local materials. To address this, Oka has even explored unconventional resources from the automotive supplier network.
The Road Ahead for American Manufacturing
For companies like Keen and Oka Brands, manufacturing shoes domestically requires a blend of investment, innovation, and patience. While there’s a growing interest in local production—partially spurred by recent tariffs and pandemic-driven supply chain disruptions—Harward expresses skepticism about whether tariffs alone will significantly change the current landscape. “It would probably take 10 years of pretty high tariffs,” he notes, with a cautious prediction that only about 6% of production may realistically shift back to the US.
As Keen moves forward with its plans, the company exemplifies the type of long-term investment decisions that family-owned businesses can make, free from the pressures of quarterly financial results. “We are a private, values-led company,” Perumal adds, emphasizing their commitment to sustainable manufacturing.
Conclusion: A Future of Technology and Tradition
Keen’s new manufacturing venture does not signify a return to the past, but rather hints at the future of American manufacturing—where innovation through technology meets traditional crafting methods. As the landscape continues to evolve, the challenge remains for the industry to navigate the complexities of reshoring while maintaining efficiency and profitability.
Company | US Production (% of Total) | Main Production Locations |
---|---|---|
Keen | 9% | Kentucky, Asia |
Oka Brands | 100% | Georgia, USA |
Nike | Unknown | Global |
Adidas | Unknown | Global |